- Vehicle design and performance depend on aerodynamics, which is a critical factor that we need to consider. The shape of the car determines various parameters such as drag, lift, and stability and even the efficiency of fuel. As regulatory requirements on emissions have tightened and consumers call for vehicles that use less fuel, car manufacturers are turning to CFD simulation during the design process of automobiles.. CFD allows engineers to conduct advanced aerodynamic analysis virtually and optimize designs to reduce drag. In this article, we will explore how computational techniques are being used by manufacturers to study airflow behavior, validate designs and enhance car aerodynamics. We will discuss the key factors impacting drag forces and the analysis of different vehicle models. The processes of CFD simulation, validation against experimental data and sensitivity studies will also be covered.
Computational Fluid Dynamics Analysis
CFD is an efficient and accurate computational numerical technique which can be used for modeling and analysis of fluids and their surrounding structures. Computational fluid dynamics is a discipline of science that involves the use of mathematical models and numerical techniques to tackle challenges that involve fluid velocities. In CFD, the fluid domain is divided into smaller sections called meshes. Then governing equations describing the fluid flow, heat and mass transfer behavior, and related phenomena are discretized and solved iteratively to obtain values of pressure, velocity, temperature etc. at different points within the domain. By analyzing the results, engineers can understand how fluids behave and interact with surfaces defined by boundary conditions. CFD finds applications in design and analysis of products involving fluid dynamics like aircraft, cars, pumps, turbines etc. It helps in optimizing designs while reducing time, costs and physical testing requirements.
Factors Affecting Aerodynamic Drag
In this section, we will discuss the factors that affect aerodynamic drag:
Vehicle Shape
Streamlined shapes with smooth, gradual contours experience less drag compared to bluff, abrupt shapes. Rounder shapes are better than sharp edges.
Surface Texture
Rough textures induce turbulence and separation increasing drag. Smooth polished surfaces experience less turbulence.
Cross-sectional Area
A smaller frontal cross-section presents less resistance. Tapering and narrowing bodies reduces drag.
Speed
Drag force increases exponentially with speed due to its velocity-squared dependence. Higher speeds experience significantly more drag.
Boundary Layer Separation
Profiles causing early boundary layer separation generate higher pressures on the rear increasing drag. Delaying separation reduces drag.
Fluid Properties
Denser fluids like water offer more resistance than gasses. Compressible flows experience greater drag at supersonic speeds due to shock waves.
Add-ons and Protrusions
External attachments, mirrors, and antennas add to the wetted area and form drag. Fewer external components reduce aerodynamic drag.
Analysis of different vehicle models:
Vehicle manufacturers put vehicles through rigorous testing and analysis to improve their designs for better efficiency and performance. Aerodynamic drag analysis gives valuable insights into how the atmosphere interacts with the vehicle’s shape. Compact and sedan models tend to have lower drag coefficients than SUVs and trucks due to their streamlined frames. Sports cars are optimized for high speed with precise shaping, wide tracks, and low ground clearance for steady handling at velocities over 200 kph. Drag analysis also helps electric vehicles maximize range by reducing energy lost to air resistance. Continuous analysis of new models helps auto companies build increasingly efficient vehicles.
Validation of CFD Results
CFD simulations need to be validated by comparing numerical results with experimental data. Physical experiments are conducted on scale models in a wind tunnel or water tunnel to measure quantities like drag and lift forces, pressure, and velocity distributions. These experimental values are then compared with the corresponding CFD-predicted values at matching flow conditions and Reynolds numbers. Percentage error analysis is done between the two results to assess the accuracy of the simulation. Sources of error can be identified to refine simulation capabilities. Only validated simulations can be truly relied upon for engineering design and analysis applications.
Pitch Sensitivity Analysis
Pitch sensitivity analysis examines how aerodynamic forces change with increasing pitch or nose-up angle of attack. CFD simulations are run by incrementally altering the pitch angle and observing its effect on lift and drag forces. While lift generally increases with higher angles of attack, drag also rises sharply. Beyond a certain pitch, flow separation begins on the wing surfaces leading to a sudden drop in lift called stall. Stall can potentially make the aircraft unstable if recovery is not quick. Through pitch sensitivity studies, designers evaluate an aircraft’s stability and maneuvering limits to ensure safe flight over a range of operational conditions.
Conclusion
Therefore, it can be concluded that computational fluid dynamics is a vital simulation tool, which is increasingly applied in the current aircraft, automobile, and other vehicles’ designs. CFD enables engineers to simulate fluid flow and aerodynamics with great accuracy without having to construct physical models. It helps reduce design cycle time and costs compared to experimental testing. While CFD simulations provide invaluable insights, proper setting of boundary conditions, grids, solver schemes and validation against experimental data is important. Ongoing improvements in computational power and numerical algorithms are making CFD an increasingly accurate and reliable virtual testing methodology. In the future, it will be integrated even more closely with the overall vehicle development process from initial conceptualization to certification.
FAQs
What is CFD analysis?
CFD stands for computational fluid dynamics. It is a computer-based technique to simulate and analyze fluid flow problems. CFD uses numerical methods and algorithms to find approximations to the governing equations for fluid motion and heat transfer.
How does CFD help in automobile design?
CFD allows automakers to test numerous design concepts virtually before building prototypes. It helps optimize aerodynamic shape for better fuel efficiency and handling stability. Drag reduction using CFD cuts emissions and development time/cost compared to repeated wind tunnel experiments.
What are the key parameters analyzed in CFD?
Parameters like pressure, velocity, and temperature distributions are analyzed to understand airflow behavior. Forces like lift and drag are also calculated at different speeds and orientations. Automakers use CFD simulations to study flow separation, vortex formation, wake turbulence and other phenomena affecting vehicle aerodynamics.
How are CFD results validated?
Engineers conduct wind tunnel or coast-down tests to generate real-world validation data. CFD predictions are then compared against experimental results to check for percentage errors. Validated simulations provide accurate virtual testing capability before physical prototypes are built.
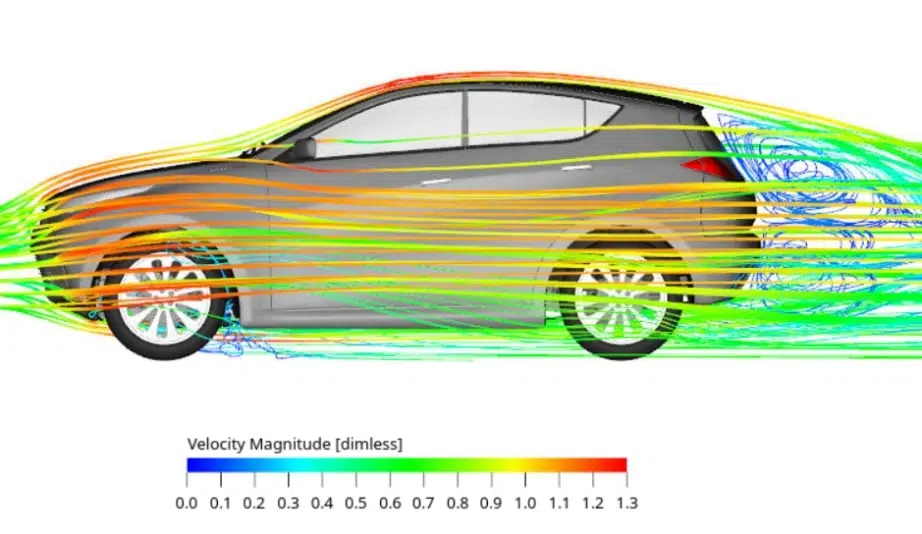